Lifting Equipment Case Study – T&E Displays
The Challenge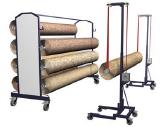
This Lifting Equipment Case Study focuses on T&E Display Group, based in Halesowen, are successful manufacturers of commercial interiors and bespoke point-of-sale display equipment. As part of the carpet display system, they supply the Yankee Roll Lifter to position carpets onto the display frame. The carpets and vinyl’s being lifted can be in excess of 300 kilos and over 2 meters from the floor. Without the Yankee, carpets would have had to be lifted manually. T&E realised that there was potential to help their clients meet their health & safety responsibilities through a safer system of work.
Andrew Fry, Managing Director of T&E, recognized that EU directives and standards could provide a path to proving due diligence had been performed before the products were placed on the market. In effect, some of their lifting and weight bearing products posed a potential risk to the business, so Andrew contacted the CE Marking Association to look at any compliance issues. In turn, we asked the West Midlands Manufacturing Advisory Service to assist T&E with matched funding for the technical assistance. This made the project very attractive and cost effective for T&E.
Andrew Fry, Managing Director of T&E Displays
While T&E were confident in the safety of the products, they had to prove it. We visited T&E within a couple of days of receiving the initial call to investigate the current state of T&E’s compliance and review the products. Options were presented, enabling T&E to select a suitable and economically reasonable pathway to compliance. As the products were elegant and simple rather than complicated, it was decided that T&E could physically test the Yankee themselves by loading and photographing the lifter. T&E agreed that some documented proof was needed to prove that due diligence had been performed. With the help of T&E and their current product specification documents, the CE Marking Association performed risk assessments as required under the machinery directive and compiled technical files that complied with the necessary requirements.
The Result
Protecting the business from claims of negligence and ensuring a safer working environment for all users. The technical files contain all relevant data on the product (relevant standards, risk assessments, bill of materials, diagrams and user guides etc.) and are probably the most important way to prove that a company has met its responsibilities. It is good practice to maintain and update your technical file whenever you make changes to your product.
For more help and advice then please call us on 01564 792349